Sasquatch_Ryda
Well-Known Member
Ford Technician
OTOTM Winner
Solid Axle Swap
Forum Staff - Retired
TRS Banner 2012-2015
- Joined
- Aug 8, 2007
- Messages
- 7,916
- Age
- 37
- City
- Terrace, BC, Canada
- Vehicle Year
- 1991
- Engine
- 4.0 V6
- Transmission
- Automatic
- Tire Size
- 40s
And it's done!
A Sterling 10.25 with a WMS to WMS measurement of 61.75"!
61.25" without drums/discs on the hubs.
I had to trim each shortside shaft 3/8" at the splines to make it all fit together.
No pictures of the actual narrowing process unfortunately... was working on this late last night and was kinda in the zone fab wise...forgot to grab my camera.
Basically what I did was bevel each cut end so I could hit it with a 3 pass weld. I made sleeves that fit inside of the axle tubes out of 1/8" wall 3" OD tube, slid them into the axle tubes 2", tack welded them then pounded the outer portion of axle shaft/spindle onto the sleeve. Trued them to eachother using a straight edge and some angle iron (Gwaii style, thanks Tom) and tack welded everything. Checked it all, and finish welded in 1" increments on opposite side to minimize warping until it was fully welded. Ground the welds smooth and blended everything so it looks like it was meant to be. Turned out pretty good.
A Sterling 10.25 with a WMS to WMS measurement of 61.75"!
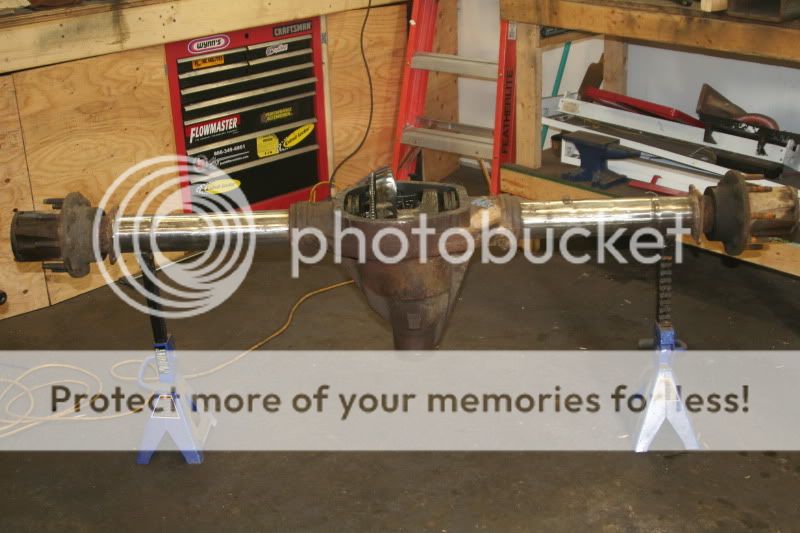
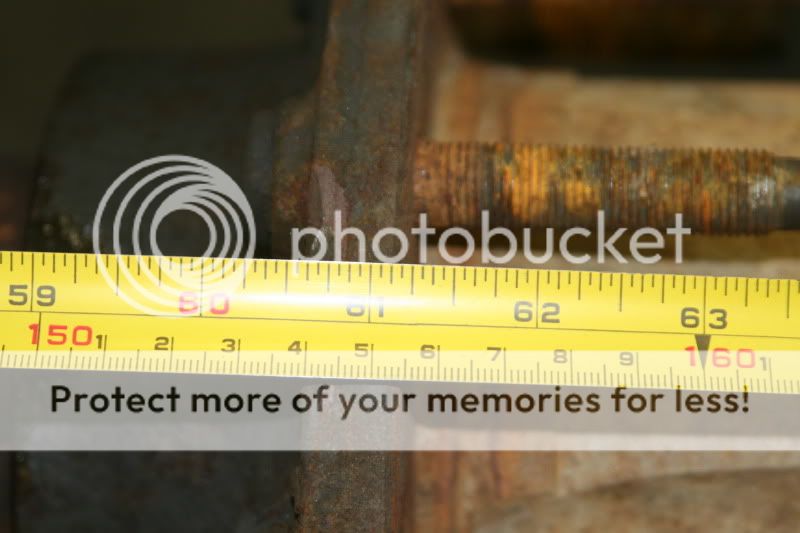
61.25" without drums/discs on the hubs.
I had to trim each shortside shaft 3/8" at the splines to make it all fit together.
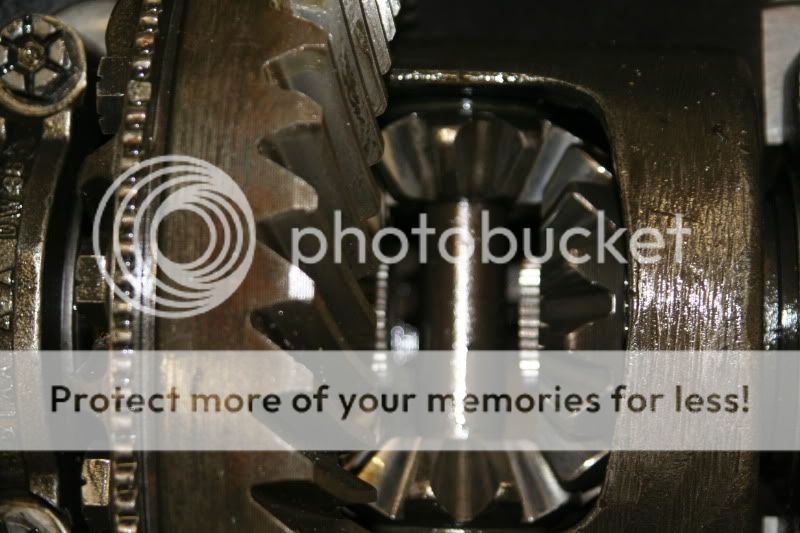
No pictures of the actual narrowing process unfortunately... was working on this late last night and was kinda in the zone fab wise...forgot to grab my camera.
Basically what I did was bevel each cut end so I could hit it with a 3 pass weld. I made sleeves that fit inside of the axle tubes out of 1/8" wall 3" OD tube, slid them into the axle tubes 2", tack welded them then pounded the outer portion of axle shaft/spindle onto the sleeve. Trued them to eachother using a straight edge and some angle iron (Gwaii style, thanks Tom) and tack welded everything. Checked it all, and finish welded in 1" increments on opposite side to minimize warping until it was fully welded. Ground the welds smooth and blended everything so it looks like it was meant to be. Turned out pretty good.