ranger_steve
New Member
- Joined
- Feb 27, 2011
- Messages
- 71
- Reaction score
- 0
- Points
- 0
- Vehicle Year
- 1993, 2007
- Make / Model
- ford
- Engine Size
- 4.0L
- Transmission
- Automatic
Well today is a snow day so I figured I'd do something productive like start my build thread. A bit of history, I'm a 19 year old electrical apprentice, I like screwing around with wires (duh) and anything mechanical. Both of my grandfathers were ford guys so I got the bug when I was young. One of them was a ford mechanic and also owns a ranger.
I bought "Bessie" in August of 2012 with somewhere around 260 xxx kms, A little high but it was my first rig and at 1800 bucks I was super excited (and broke after I purchased it haha working at a pizza joint for the summers) she now has 298,600 kms. After checking it all out and driving it up the road before buying it, dad and I figured out it needed a radius arm bushing (only to discover it needed the mount too from wearing into the steel). It also wasn't starting 100% so the guy had it checked out and bought a new solenoid for up on the fender well, I installed it when we got home. It was going to need a windshield for safety inspection too. Just before we signed the paperwork the old guy comes out of his shed with a brand new carrier bearing for the rear driveshaft!
Truck info when purchased:
1993 ranger 4x4
4.0L with auto trans
8.8 rear with 3.73LS and drums
dana 35 ttb 3.73 open
Mile marker manual hubs
Here she is a few days after I got her home and washed.
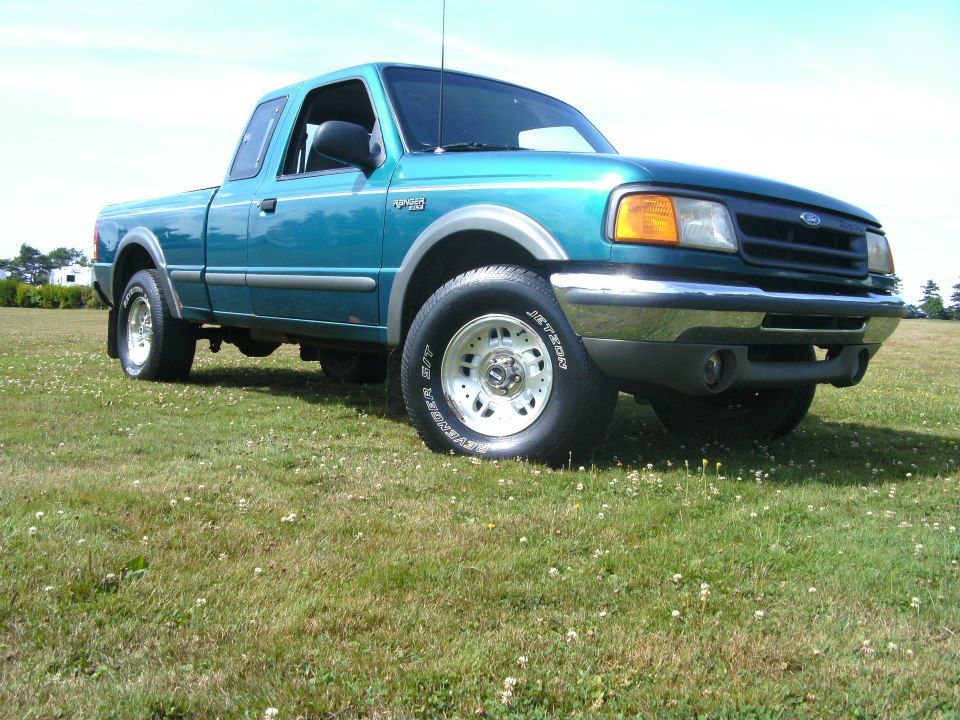
Projects Done (stage 1):
Sony deck with ipod dock
Headache rack w/ led signals/reverse and 42" led light bar
toolbox with aux battery/wiring/relays/fuses and isolator solenoid
quick connect booster cables
new body mount bushings and fixed rotten mounts
3" body lift
31" Goodyear Wranglers
Custom rear bumper with shackle mounts
On Board Air from Stock Sanden A/C Compressor, Air tank where spare tire was
Grover dump truck horns
Billet grille with spray tinted large emblem
Switch panel in center console
Thrush welded muffler (was dumped after muffler, now turndown over rear axle)
Replaced rad support
Blue led swap in instrument cluster and dome light
Swapped leaky abs diff cover for chrome plated steel one
Belltech 6400 (on low height until 2" lift on front)
To Do for stage 1.5 (near future):
2" washer coil spacers
33 x 12.5 x 15 cooper all terrains
Replace all u-joints from t-case forward
Weld spider gears in d35
Replace leaky d35 seals
Possibly replace slip joint on front axle shaft
c-clip eliminator
new wheel bearings and balljoints
Install camber bushings
Roll on Box Liner
To do for stage 2 (wayyyy down the road):
Cummins 4bt and zf5 or nv4500 and t-cases to go with whatever trans gets used
EB D44 or Narrow a full width 4.10's or 4.56's
Explorer 8.8 w/ discs and 4.10's or 4.56's
35 or 36" skins on Cragar soft 8 chromies
More pics to post tomorrow. Questions, Comments, tips etc.. feel free to let me know!
I bought "Bessie" in August of 2012 with somewhere around 260 xxx kms, A little high but it was my first rig and at 1800 bucks I was super excited (and broke after I purchased it haha working at a pizza joint for the summers) she now has 298,600 kms. After checking it all out and driving it up the road before buying it, dad and I figured out it needed a radius arm bushing (only to discover it needed the mount too from wearing into the steel). It also wasn't starting 100% so the guy had it checked out and bought a new solenoid for up on the fender well, I installed it when we got home. It was going to need a windshield for safety inspection too. Just before we signed the paperwork the old guy comes out of his shed with a brand new carrier bearing for the rear driveshaft!
Truck info when purchased:
1993 ranger 4x4
4.0L with auto trans
8.8 rear with 3.73LS and drums
dana 35 ttb 3.73 open
Mile marker manual hubs
Here she is a few days after I got her home and washed.
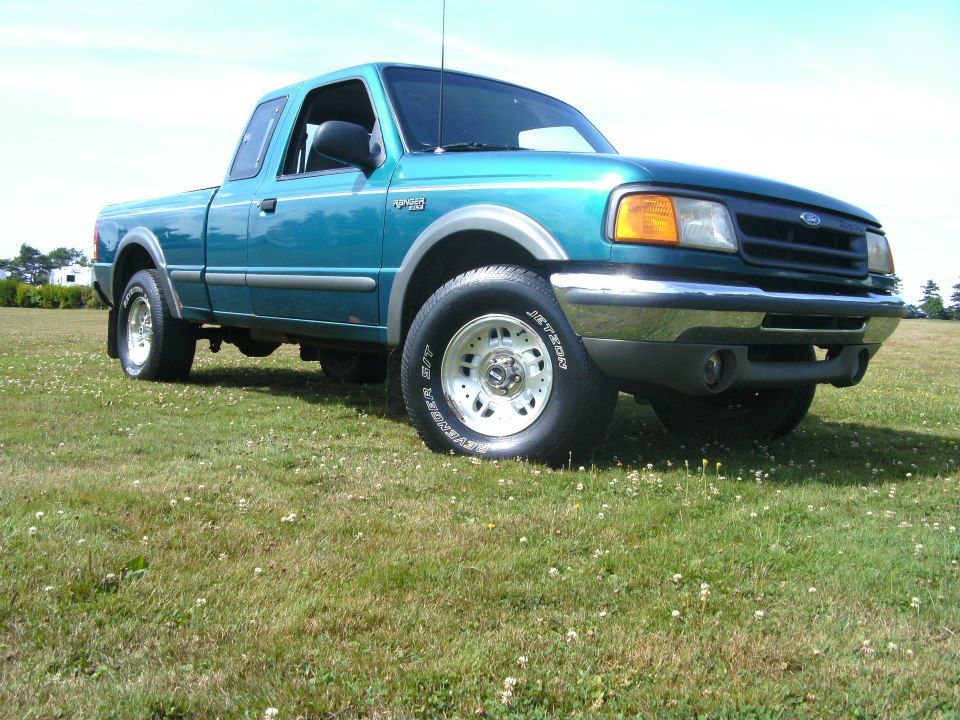
Projects Done (stage 1):
Sony deck with ipod dock
Headache rack w/ led signals/reverse and 42" led light bar
toolbox with aux battery/wiring/relays/fuses and isolator solenoid
quick connect booster cables
new body mount bushings and fixed rotten mounts
3" body lift
31" Goodyear Wranglers
Custom rear bumper with shackle mounts
On Board Air from Stock Sanden A/C Compressor, Air tank where spare tire was
Grover dump truck horns
Billet grille with spray tinted large emblem
Switch panel in center console
Thrush welded muffler (was dumped after muffler, now turndown over rear axle)
Replaced rad support
Blue led swap in instrument cluster and dome light
Swapped leaky abs diff cover for chrome plated steel one
Belltech 6400 (on low height until 2" lift on front)
To Do for stage 1.5 (near future):
2" washer coil spacers
33 x 12.5 x 15 cooper all terrains
Replace all u-joints from t-case forward
Weld spider gears in d35
Replace leaky d35 seals
Possibly replace slip joint on front axle shaft
c-clip eliminator
new wheel bearings and balljoints
Install camber bushings
Roll on Box Liner
To do for stage 2 (wayyyy down the road):
Cummins 4bt and zf5 or nv4500 and t-cases to go with whatever trans gets used
EB D44 or Narrow a full width 4.10's or 4.56's
Explorer 8.8 w/ discs and 4.10's or 4.56's
35 or 36" skins on Cragar soft 8 chromies
More pics to post tomorrow. Questions, Comments, tips etc.. feel free to let me know!
Last edited: